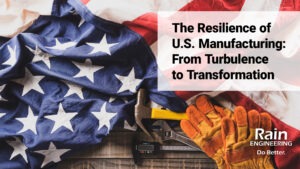
The Resilience of U.S. Manufacturing: From Turbulence to Transformation
The Resilience of U.S. Manufacturing: From Turbulence to Transformation U.S. manufacturing has long been a cornerstone of economic strength and innovation, shaping the nation’s prosperity