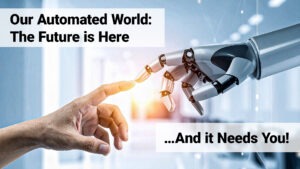
Our Automated World: The Future is Here (… And it Needs You!)
Our Automated World: The Future is Here (… And it Needs You!) AI and automation are no longer creeping into manufacturing—they’ve arrived, settled in, and
AI and automation are no longer creeping into manufacturing—they’ve arrived, settled in, and started rewriting the rules.
From predictive maintenance to robotic arms that work side by side with humans, the shift is undeniable.
And for the people who’ve spent years—sometimes decades—working the factory floor, this isn’t just a change in technology, it’s a change in what it means to be a skilled worker, ultimately, reshaping how work gets done.
So, what does this mean for those workers at the center of it all?
Today, we dive into the steps today’s workers should be taking to make sure they continue to be a valuable asset in an industry that is moving forward (whether they like it or not.)
Let’s start with the fear—because it’s real, and pretending it isn’t doesn’t help anyone.
The mention of automation often triggers anxiety: Will I be replaced? Will my job disappear?
But the reality is more nuanced.
Automation isn’t about removing people from the equation. It’s about redefining their role.
Instead of fearing machines, today’s workers need to start viewing them as tools—tools that, like any others in a skilled trade, must be understood, maintained, and optimized.
Once that mental shift happens, the path forward becomes clearer.
This isn’t the end of the line—it’s a fork in the road. Workers can either resist and get left behind or lean in and become part of something bigger.
The good news?
This isn’t about starting from scratch.
Manufacturing workers already have a solid foundation in discipline, process thinking, and attention to detail.
Those traits are incredibly valuable in the new era of automation.
What’s required now is a willingness to learn how to apply those strengths in new ways.
The heart of this shift is technology—but that doesn’t mean workers need to become programmers or data scientists.
What they do need is tech literacy: the ability to understand how machines think, how systems communicate, and how to navigate digital interfaces that are becoming as common as the wrench once was.
Whether it’s interacting with a digital dashboard, understanding alerts from a predictive maintenance system, or working alongside a collaborative robot, these tools are fast becoming part of everyday work.
And just like a new piece of machinery, they require training, patience, and practice.
Fortunately, that training doesn’t have to mean going back to school or earning a new degree.
Many companies are offering in-house learning programs, and there’s no shortage of online resources – like Manufacturing KnowHow from Rain Engineering – tailored specifically to manufacturing tech and your schedule.
The key is staying curious and open.
Workers who regularly challenge themselves to learn something new—no matter how small—are building the muscle memory they’ll need to adapt again and again.
It’s time to retire the idea that machines and humans are in a zero-sum game.
Automation isn’t replacing humans—it’s shifting their focus.
Take collaborative robots, or cobots, as an example.
These machines are designed to work alongside people, not instead of them.
They handle the dull, dangerous, and repetitive tasks, allowing workers to focus on higher-level responsibilities.
In this kind of environment, the value of human labor changes—but it doesn’t disappear.
Workers become process overseers, troubleshooters, quality control experts, and systems thinkers.
And when a system falters or an unexpected problem arises, it’s still the human eye, judgment, and experience that solves it.
That’s the future of manufacturing: humans and machines working TOGETHER.
The cobot doesn’t have intuition. It can’t recognize a subtle change in material consistency. It can’t spot the early warning signs of a malfunction that aren’t captured by data, but a trained, experienced worker can!
… And when that worker also understands how the machine operates, the real value is found.
The best way for workers to stay relevant is to become lifelong learners.
That doesn’t mean constantly being in formal training—it means making learning part of the job.
Asking questions. Staying curious. Engaging with new tools instead of avoiding them. And seeking out opportunities to learn from others—whether through mentorship, peer collaboration, or industry events.
But learning isn’t just an individual responsibility.
Manufacturers themselves have a role to play in making education accessible and in building a culture where change is embraced, not feared.
When companies invest in training, invite feedback, and involve workers in the innovation process, adoption of new technologies goes smoother for everyone.
Workers who feel included in the conversation are more likely to participate in the change—and to drive it.
They become internal champions for technology, helping their peers adapt and helping leadership spot real-world challenges that only hands-on workers would notice.
To adapt effectively, workers need to keep their eyes on the horizon.
The transformation of manufacturing is part of a broader industrial shift—Industry 4.0.
That means smarter factories, integrated systems, and data flowing from every corner of the production line.
Workers who stay engaged with industry trends will have a better sense of what skills they’ll need next.
Whether that means learning to work with MES (Manufacturing Execution Systems), understanding the basics of data interpretation, or getting comfortable with mobile-based plant monitoring, being aware of what’s coming makes it easier to stay ahead.
Reading trade publications, participating in webinars, talking with suppliers, or even just asking questions during meetings—all of these actions help workers remain connected.
The more informed they are, the more confident and capable they’ll feel navigating this evolving landscape.
Folks, the automation era isn’t something we’re waiting for. It’s here!
But this isn’t the end of the line for the manufacturing workforce—it’s the beginning of something entirely new.
A smarter, more connected, more resilient workforce is emerging—one where human insight, digital fluency, and adaptability define success.
… And for workers willing to evolve, this moment is full of possibility.
Not everyone will take that step—but those who do won’t just survive automation… They’ll become the people who lead it.
P.S. At Rain Engineering, we understand that the rise of automation isn’t about replacing your workforce—it’s about empowering it.
We know the factories of tomorrow will be built not just on machines, but on insight, adaptability, and smart system integration.
That’s where we come in…
Whether you’re introducing robotics to your production line, implementing MES platforms to bring clarity to your data, or navigating the complexities of Industry 4.0, Rain Engineering partners with you every step of the way.
We design automation strategies that make sense—not just for your equipment, but for your people.
Why?
Because we truly believe technology works best when it’s human-centered.
So, let’s modernize your operations, upskill your team, and create a manufacturing environment where innovation and experience work side by side.
Our Automated World: The Future is Here (… And it Needs You!) AI and automation are no longer creeping into manufacturing—they’ve arrived, settled in, and
Rare Earth Minerals and the Manufacturer’s Dilemma: How Global Politics and Critical Materials are Shaping the Future of American Industry In today’s industrial landscape, manufacturers
Manufacturing’s Quiet Crisis: The Generational Divide That’s Reshaping Industrial Work The manufacturing industry is standing on the edge of a transformation that reaches far beyond
Ready to Explore the Future of Manufacturing? As global markets become more volatile and customer demands shift faster than ever, manufacturers are at a critical
Trade Tensions Reloaded: What the Rising US-China Tariff War Could Mean for Manufacturers If you’re a U.S. manufacturer, you’ve already weathered your fair share of
Industry 4.0: A Win for Your Business and Your Workforce The manufacturing sector has always been the backbone of economies worldwide, but the current landscape